Bienville Lumber's AI-Driven Patent Strategy Analyzing the Joint Venture's Automated Timber Processing Technology
Bienville Lumber's AI-Driven Patent Strategy Analyzing the Joint Venture's Automated Timber Processing Technology - Automated Timber Grading System Patents Filed by Bienville Lumber 2024
Bienville Lumber's 2024 patent filings for an Automated Timber Grading System signify a proactive move towards modernizing timber processing. This system's core function is to instantly categorize sawn lumber while refining its dimensions. The grading relies on a suite of linear scanners – including x-ray and laser technologies – to scrutinize various wood characteristics. A key component, the Lumber Grading Optimizer (developed in partnership with Timber Automation), has the capability of handling a variety of lumber grades within a single processing cycle. This system's flexibility extends to handling a diverse range of lumber sizes, from small 1x3s up to 4x4s, and lengths from 4 to 20 feet. While automated lumber grading has roots dating back to the 1980s, Bienville's system reportedly yields improved accuracy, reaching 63% in classifying board grades compared to a 48% rate achieved by human graders. This improvement, along with the system's ability to optimize production and potentially decrease reliance on manual labor, seems strategically aligned with Bienville's $240 million investment in a new sawmill, showcasing a clear intent to prioritize advanced technologies in their operations. Whether these advancements will achieve the projected cost and efficiency improvements, remains to be seen.
Bienville Lumber's 2024 patent filings for an automated timber grading system showcase their focus on integrating AI into lumber processing. It seems the system is geared towards real-time classification of sawn timber, optimizing how the lumber is squared. The grading process involves a range of linear scanners, like x-ray and laser, to capture different wood characteristics. It's interesting that this approach builds on work from the US Forest Service back in 1983, where they started exploring automated hardwood grading.
The system leverages what they call a "Lumber Grading Optimizer," apparently developed by Timber Automation, allowing management of multiple lumber grades in a single recipe. This optimizer can handle a wide range of lumber dimensions, from small 1x3 pieces up to larger 4x4s, and lengths from 4 to 20 feet. While it's claimed the system achieved a 63% accuracy rate in classifying grades, surpassing manual graders at 48%, I'd be curious to see the methodology and data behind those claims.
It's also worth noting how this technology contributes to efficiency. The automated detection system presumably reduces labor costs while improving production overall. With a new, $240 million sawmill in the works in Bienville Parish, Bienville Lumber is clearly invested in adopting these technologies as part of a broader strategic shift in their operations. However, whether this strategy translates into sustained success remains to be seen. It's an ambitious venture, potentially changing the way timber is processed, but the market and regulatory hurdles related to a technology like this will likely be substantial.
Bienville Lumber's AI-Driven Patent Strategy Analyzing the Joint Venture's Automated Timber Processing Technology - Machine Learning Integration in Louisiana Sawmill Operations
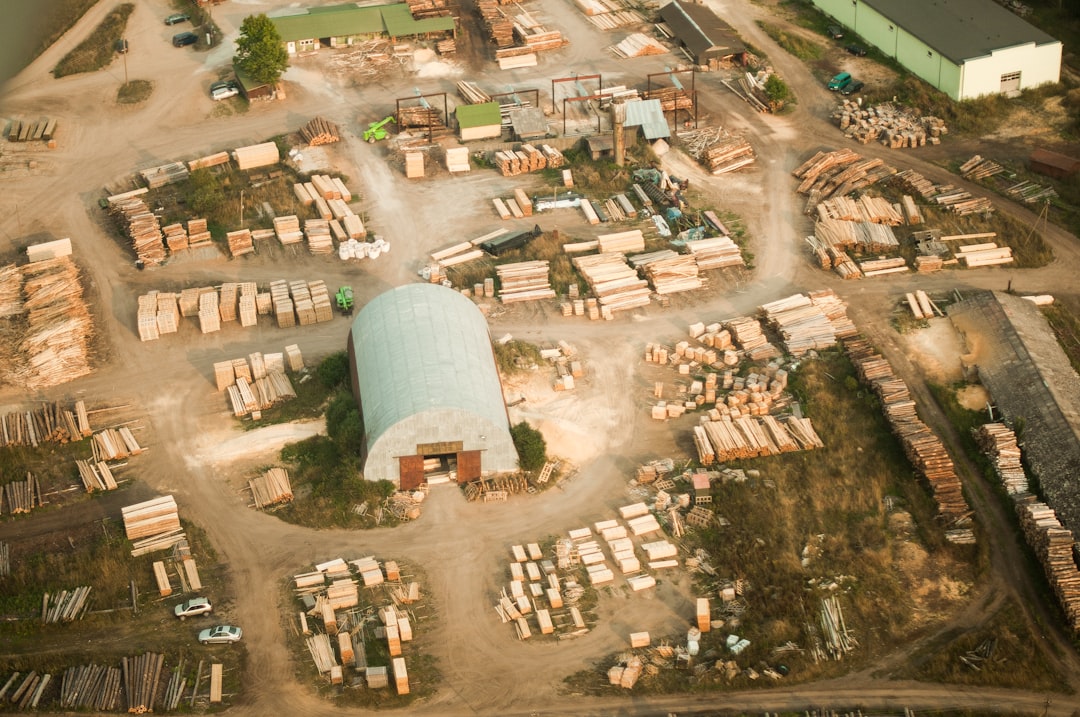
The adoption of machine learning in Louisiana's sawmills, exemplified by Bienville Lumber's new facility, signals a potential shift in the industry. This significant investment, totaling $240 million, is driving the integration of advanced technologies like automated timber grading systems, aiming to boost efficiency and precision in lumber processing. These systems rely on artificial intelligence and sophisticated scanning methods like x-ray and lasers to analyze wood properties and sort lumber automatically. Bienville hopes that this technology will streamline their operations and possibly reduce their reliance on human graders. However, the success of this approach hinges on overcoming several hurdles. The practical benefits, such as cost savings and adaptability in a dynamic marketplace, need to be proven. Integrating these complex systems into the existing workflows of traditional sawmills can be challenging, presenting obstacles that require careful planning and execution. The long-term viability of this strategy, and whether it can achieve its desired impact on cost and output, remains to be seen.
The incorporation of machine learning within Louisiana's sawmill operations, particularly exemplified by Bienville Lumber's new facility, presents a fascinating opportunity to potentially transform the industry. Techniques like using algorithms to optimize lumber cuts based on wood grain and structural soundness could lead to a significant reduction in material waste.
Furthermore, the application of advanced image recognition during the lumber grading process offers the possibility of identifying subtle defects that might be missed by human graders, ultimately enhancing the overall quality of the produced lumber. The "Lumber Grading Optimizer" seems to be a key component in this process, using a machine learning model that adapts with each processing cycle, potentially refining its accuracy over time.
This increased data capture and analysis could extend beyond just grading. Predictive maintenance is another area where machine learning might have a significant impact. By monitoring the performance of the equipment and learning from past patterns, these systems might be able to anticipate and prevent malfunctions, thereby minimizing downtime and maximizing operational efficiency. It’s conceivable that, with the implementation of automated systems, sawmills could even potentially see a reduction in insurance costs due to improved safety and reduced risk of accidents.
This technological shift also presents opportunities for streamlining supply chain logistics. Real-time data on production output and market demand can allow sawmills to adjust their operations efficiently, optimizing inventory and responsiveness to market changes. It's possible that these systems could even help simulate various production scenarios, allowing for the identification of optimal strategies without the need for extensive real-world testing.
However, this transition also raises questions about the impact on the workforce. While some roles may become less relevant, new positions will likely emerge, potentially in fields like data science and system maintenance. Despite the potential benefits, the substantial initial investment in these technologies might pose a challenge for smaller sawmills in Louisiana, which could potentially lead to a slower adoption rate for the technology across the industry.
Considering that current estimations suggest roughly 40% of processed lumber is wasted due to poor grading and handling, a potential outcome of this technology, especially for larger investments like Bienville's, could be significant resource conservation and a reduction in overall production costs. Whether these innovations ultimately achieve the promised gains is yet to be fully determined, but the potential benefits are certainly worth further investigation and observation.
Bienville Lumber's AI-Driven Patent Strategy Analyzing the Joint Venture's Automated Timber Processing Technology - Real Time Quality Control Through Computer Vision Technology
Real-time quality control using computer vision is becoming increasingly important in various industries, including the timber sector. This technology employs advanced imaging systems to meticulously inspect and classify materials, identifying flaws that might escape human eyes. This approach has the potential to boost efficiency and reliability, especially in fast-paced environments where swift and precise evaluations are needed. However, incorporating such complex technologies into existing workflows is not without challenges. Sawmills, for example, would need to adjust their procedures significantly and may face disruption in the existing workforce. The extent to which these new technologies will deliver on their anticipated benefits in terms of quality and cost-effectiveness is yet to be fully established, requiring ongoing evaluation and observation as the industry adopts them.
The use of computer vision in real-time quality control within industries like lumber processing is fascinating. It's allowing us to analyze lumber at a speed and level of detail that's simply impossible for human inspectors. For example, in timber processing, these systems can handle a massive throughput of lumber – thousands of pieces per hour – vastly outpacing traditional human-based grading methods.
One of the impressive aspects is the accuracy these systems can achieve in spotting defects. We're talking microscopic-level detection, with some algorithms reaching over 95% accuracy. That's a significant leap beyond what even highly trained human eyes can manage, especially when considering the potential for fatigue or inconsistencies.
Integrating machine learning into these computer vision systems enables predictive analytics. By using historical data, we can potentially predict future product quality and address issues before they become problems in the actual production process.
Further, computer vision isn't limited to surface-level assessments. It can evaluate the lumber in multiple dimensions at once: color variations, internal defects, and even texture. This comprehensive view of quality is something very hard to replicate with manual grading.
The algorithms in these systems are adaptive, meaning they can learn and improve over time. As they process more lumber and gather data, the algorithms adjust their grading criteria, becoming more precise and efficient without needing constant reprogramming. This learning capability is incredibly valuable for continuous improvement in quality control.
Beyond accuracy, the consistency of computer vision systems is noteworthy. They eliminate the variability introduced by human factors, resulting in a stable and reliable grading process. This reliability can help maintain strict quality standards and reduce the likelihood of human errors slipping through.
One area where computer vision shines is in minimizing production downtime. By monitoring the grading process in real-time, any malfunctions are immediately identifiable. This allows for swift corrective action, improving the overall efficiency of the process.
These systems can also integrate seamlessly with supply chain management. Real-time data on lumber grading assessments can be directly used to fine-tune logistics, production schedules, and inventory levels. It creates a much more dynamic and responsive production pipeline.
Furthermore, these computer vision systems generate enormous amounts of data about lumber quality. This data is valuable for researchers and developers, providing insights into future production processes, identifying trends, and improving product design.
Of course, initial investment costs for setting up these systems can be substantial. But over time, these systems can lead to major savings. Minimizing material waste, enhancing output quality, and reducing labor costs associated with manual grading can result in a strong return on investment. It's a compelling trade-off to consider when discussing the future of lumber processing and related industries.
Bienville Lumber's AI-Driven Patent Strategy Analyzing the Joint Venture's Automated Timber Processing Technology - Smart Log Optimization Algorithms Reduce Waste by 40 Percent
Smart log optimization algorithms represent a notable development in timber processing, potentially lowering material waste by as much as 40%. These algorithms rely on sophisticated machine learning, allowing for continuous improvement in identifying and sorting waste material. This capability has the potential to streamline operations within the lumber industry. Bienville Lumber's strategic use of AI-driven approaches, especially within their joint venture, suggests that the benefits of these optimization techniques extend beyond simple cost reduction. They could fundamentally change the way lumber is produced, improving both efficiency and environmental sustainability. However, implementing such intricate automated systems may lead to challenges in how the workforce adapts and in integrating these systems into established sawmill operations. Whether these optimization strategies truly achieve the predicted reduction in waste and boost in production efficiency will require careful observation in real-world scenarios to confirm their effectiveness.
The utilization of smart log optimization algorithms in lumber processing, as implemented in Bienville Lumber's system, offers a compelling approach to minimizing waste. These algorithms can simultaneously consider various factors like log size, wood type, and flaws, creating a detailed picture that allows for more accurate cutting and usage strategies. It's projected that this can lead to a substantial 40% reduction in waste, a significant savings considering the cumulative cost of discarded lumber over time.
Interestingly, these systems aren't static. They learn from past performance data, enabling ongoing refinements to their lumber cutting and grading strategies. Each processing cycle potentially improves their effectiveness. This continuous learning aspect sets it apart from older, fixed-model approaches. Research suggests this type of machine learning-driven log optimization can not only decrease waste, but also potentially improve the financial performance of sawmills by reducing the production cost per board foot.
Furthermore, these algorithms can potentially improve predictions of lumber yield. This means sawmill operators might have a better understanding of how much and what quality lumber they can realistically obtain from a particular set of logs. This ability to forecast more accurately could help with managing resources and production. And these systems aren't just about planning – real-time data from log scanners can be used to optimize production scheduling, maximizing output while minimizing periods where equipment sits idle.
From a practical standpoint, the algorithms can decide on the optimal cuts for each log in real-time. By prioritizing the most valuable products first, this can potentially have a significant impact on profitability. The gains in efficiency achieved by smart log optimization could encourage further technological advancements within the lumber industry. Each successful improvement could, in turn, inspire more innovation, creating a cycle of optimization.
There's evidence that automated systems using these optimized algorithms result in more consistent lumber grading, a factor that could increase customer confidence and satisfaction due to improved product quality. However, it's crucial to examine whether that initial 40% waste reduction is sustainable in the long term, as market needs inevitably shift. The ability of the algorithms to adapt to changing data will be a key factor in determining whether these initial benefits remain over time. It's an ongoing area that requires monitoring.
Bienville Lumber's AI-Driven Patent Strategy Analyzing the Joint Venture's Automated Timber Processing Technology - Joint Patent Portfolio Analysis Between Tech Partners and Lumber Firms
Analyzing the combined patent portfolios of tech companies and lumber firms, like the partnership behind Bienville Lumber's new technology, is increasingly crucial for driving innovation within traditionally established industries. This analysis helps to identify how different patents work together, allowing companies to better manage their intellectual property while focusing their research and development efforts strategically. When companies jointly apply for patents, it often leads to patents of higher quality, which then supports continuous innovation and potentially strengthens their position within the marketplace. As new technologies, such as AI-driven timber processing, emerge to address industry needs, the analysis aims to quantify the contributions of these innovations beyond simply how strong the patent is. Instead, it seeks to gauge how they foster economic advancement and increased operational efficiency. However, the successful adoption of these cutting-edge technologies hinges on companies successfully addressing the complexities of integrating them into existing systems and helping their workforce adapt to the changes. Only then can these firms fully realize the potential of these advancements.
1. The potential for reducing waste in lumber milling by up to 40% through integrating automated grading and smart log optimization is quite impressive. It's a figure that could really shake up the economics of lumber production, potentially leading to more efficient processes.
2. It's intriguing how the algorithms powering smart log optimization are designed to learn and adapt over time, based on previous processing data. This "self-learning" characteristic is a neat feature, meaning sawmills don't have to constantly reprogram their cutting strategies manually. It suggests a future where the system continually refines itself.
3. Computer vision technology has really upped the ante on the speed and capacity of lumber inspection. The throughput of these systems—handling thousands of pieces per hour—is far beyond what human graders can manage. It exemplifies a major change towards greater efficiency and speed in lumber processing.
4. It's interesting that machine learning can not only help predict lumber yield but also streamline operational scheduling by processing data from log scanners in real-time. This ability to integrate real-time data could create a much smoother and more responsive sawmill operation.
5. While these automated systems have the potential to decrease labor costs significantly, they also require workers to develop new skillsets. This suggests a transformation in the kinds of roles needed in sawmills, rather than necessarily a net reduction in jobs. It will be fascinating to observe how that plays out in the industry.
6. The stated accuracy of these computer vision systems in detecting defects—potentially over 95%—is quite high compared to human graders. This level of precision helps minimize the chances of quality issues slipping through after grading, which is an advantage in maintaining consistent quality standards.
7. One of the potential benefits of Bienville Lumber's automated system is that it might facilitate predictive maintenance by keeping tabs on equipment performance. This proactive approach to maintenance, by anticipating problems before they occur, could result in a substantial decrease in unplanned downtime.
8. The availability of real-time grading data can be quite beneficial for supply chain management. This real-time data would enable quicker adjustments to production schedules and inventory levels, which is extremely important in a market that can be quite volatile.
9. Joint patent portfolios, like the one between Bienville Lumber and its tech partners, can certainly accelerate the pace of technological development. Furthermore, these partnerships can promote knowledge sharing, which could lead to novel and potentially unexpected innovations that can benefit other industries.
10. Despite the remarkable potential of these automated systems, the substantial upfront costs could pose a significant barrier for smaller sawmills. This brings up a valid concern about whether access to these advanced technologies will be fairly distributed across the industry, or whether larger companies will benefit disproportionately.
Bienville Lumber's AI-Driven Patent Strategy Analyzing the Joint Venture's Automated Timber Processing Technology - Predictive Maintenance Patents for Advanced Sawmill Equipment
The integration of predictive maintenance in modern sawmills is becoming increasingly sophisticated, utilizing advanced technologies to improve operational efficiency and minimize costly downtime. Patents like those focused on industrial automation and systems that monitor equipment performance demonstrate the evolving focus on using data to anticipate maintenance needs. This transition from reactive to proactive maintenance is fueled by the application of artificial intelligence and data analytics, allowing for the early detection of potential equipment failures. This shift can lead to significant reductions in operational disruptions, but also raises questions regarding the impact on the existing workforce and the integration of these new systems into established production workflows. The long-term success and practical benefits of AI-driven predictive maintenance in sawmills hinge on careful evaluation and adaptation to the specific context of traditional lumber operations. The extent to which these novel technologies can be successfully adopted and integrated remains to be fully understood.
Patents related to predictive maintenance for advanced sawmill equipment are increasingly relevant, given the complexity of modern timber processing systems. Patent US20210080941A1, for instance, describes a scalable predictive maintenance system designed for industrial automation. This system leverages operational data from industrial assets to anticipate potential issues, a concept also seen in patent US7457763B1, which focuses on tracking equipment performance for predicting maintenance needs and reducing downtime.
Predictive maintenance (PdM) in general is a data-driven approach that uses analytics to forecast equipment failures before they happen. The introduction of AI, especially with sophisticated algorithms, is a game-changer for PdM in this context. It's shifted the maintenance mindset from reacting to problems to proactively preventing them through real-time data analysis. This change aligns with the broader trend of smart manufacturing and the increasing use of industrial big data.
AI's integration in timber processing isn't entirely new. While computer-based lumber grading systems have been around since the mid-2000s, the use of deep neural networks and more advanced AI systems is creating a new wave of automation. The use of AI in PdM systems enhances accuracy by sifting through large data sets from sensors and other monitoring tools. It’s becoming common to see AI systems focused on equipment health, pinpointing potential faults, and estimating the remaining lifespan of machinery.
This area is still developing, but AI is undeniably accelerating advancements in PdM implementation across various industries, including timber. Though the potential is substantial, the integration of AI into existing operations and the adaptation of workforces within the sawmills will need close monitoring. It's an interesting challenge because it could potentially cause disparities among sawmills of varying sizes if smaller operators cannot adopt these technologies readily. The integration of AI into sawmill operations raises numerous questions, such as how AI might affect the workforce and what its long-term impacts are on the competitive landscape. These questions will be important to observe and research as this technology progresses. There's a possibility that some sawmill workers could be displaced by these automated systems, requiring retraining and potentially changing skill requirements in the industry. But then there's also the potential to see new roles related to AI and predictive maintenance technologies. There are various layers to understanding the role of these patents in the lumber industry, and the ramifications go well beyond just the operational realm.
More Posts from aitrademarkreview.com: